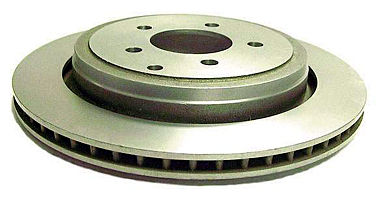
Objectifs :
L'apprenant sera en mesure :
- de citer les principaux avantages et les limites d'utilisation dans la réalisation de pièces et de structures en MCMM,
- de citer les intérêts intrinsèques de ces matériaux et les avantages par rapport aux composites à matrice organique et aux alliages métalliques,
- de décrire succinctement les deux grands types de principes de fabrication.
Les matériaux composites à matrice métallique (MCMM) possèdent des avantages par rapport aux matériaux composites à matrice organique (MCMO) :
- une meilleure stabilité dimensionnelle ;
- une température d'utilisation plus élevée ;
- des méthodes d'assemblage plus simple, similaires à celles des métalliques.
Ils possèdent également des avantages par rapport aux métaux :
- une meilleure durée de vie en fatigue ;
- des propriétés mécaniques spécifiques plus élevées ;
- une stabilité dimensionnelle améliorée.
Trois domaines d'intérêt des MCMM ont été identifiés :
- les pièces massives des structures froides dimensionnées en rigidité ;
- les structures moyennement chaudes (températures comprises entre 150°C et 500°C) ;
- les structures dimensionnées en stabilité dimensionnelle, les MCMM étant insensibles au vieillissement humide.
On distingue plusieurs technologies de fabrication :
- la voie liquide (moulage-forgeage, fonderie basse pression) ;
- la voie solide (métallurgie des poudres) ;
- la technologie des préimprégnés : le soudage diffusion (diffusion - Bonding).
En voie liquide, le moulage-forgeage (fonderie haute pression) endommage la préforme du renfort.
La fonderie basse pression est moins endommageant et moins coûteuse.
En voie solide, la métallurgie des poudres permet d'obtenir un matériau plus performant.
La technologie des préimprégnés se rapproche beaucoup de celle employée pour les MCMO : un empilement de préimprégné souple métallisé et pressé à chaud pour être mis à la forme.
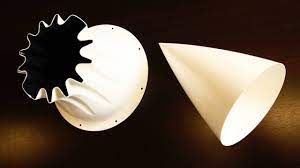
Objectifs :
L'apprenant sera capable :
- de citer les principales catégories de renfort et matrice utilisées,
- de décrire succinctement les principales possibilités de fabrication,
- de préciser les principaux avantages et les limites des céramiques renforcées et des carbone/carbone.
Résumé :
Les composites thermostructuraux sont divisés en trois sous-familles :
- les céramiques armées ;
- les carbone/carbone ;
- les composites à matrice métallique.
Les principaux critères recherchés sont notamment :
- la réfractarité ;
- la résistance thermomécanique ;
- la stabilité dimensionnelle.
Les composites céramiques renforcées s’obtiennent par trois procédés d’imprégnation :
- la voie gazeuse ;
- la voie liquide ;
- la voie solide.
Les procédés peuvent se combiner pour obtenir les caractéristiques voulues à moindre coût. De plus, la grande fragilité (intrinsèque aux céramiques) amènent les fabricants à développer des solutions d’auto-cicatrisation pour limiter cet inconvénient.
Les applications des composites céramiques particulaires sont principalement les prothèses de hanche et les plaquettes des outils de coupe. Les applications des composites céramiques à renforts longs sont principalement des pièces de structure et des protections thermiques soumises à des températures de l’ordre de 1500°C, ainsi que des pièces des systèmes de freinage automobile pour leur performance en gain de masse et en durabilité.
Les composites carbone/carbone s'obtiennent par trois procédés d'imprégnation :
- liquide basse pression et basse température ;
- en phase gazeuse ;
- liquide haute pression et haute température.
La première méthode présente des défauts. La seconde demande beaucoup de temps (plusieurs semaines). Le meilleur compromis est la troisième méthode, très utilisée pour les pièces subissant de fortes contraintes thermiques et soumises à l'ablation.
Le composite carbone/carbone est essentiellement utilisé pour des applications nécessitant une tenue mécanique à de hautes températures pendant de longues durées (par exemple : protections thermiques) et des applications demandant la conservation d’un comportement tribologique satisfaisant dans des conditions de température extrême (de l’ordre de 2000 à 3000°C).
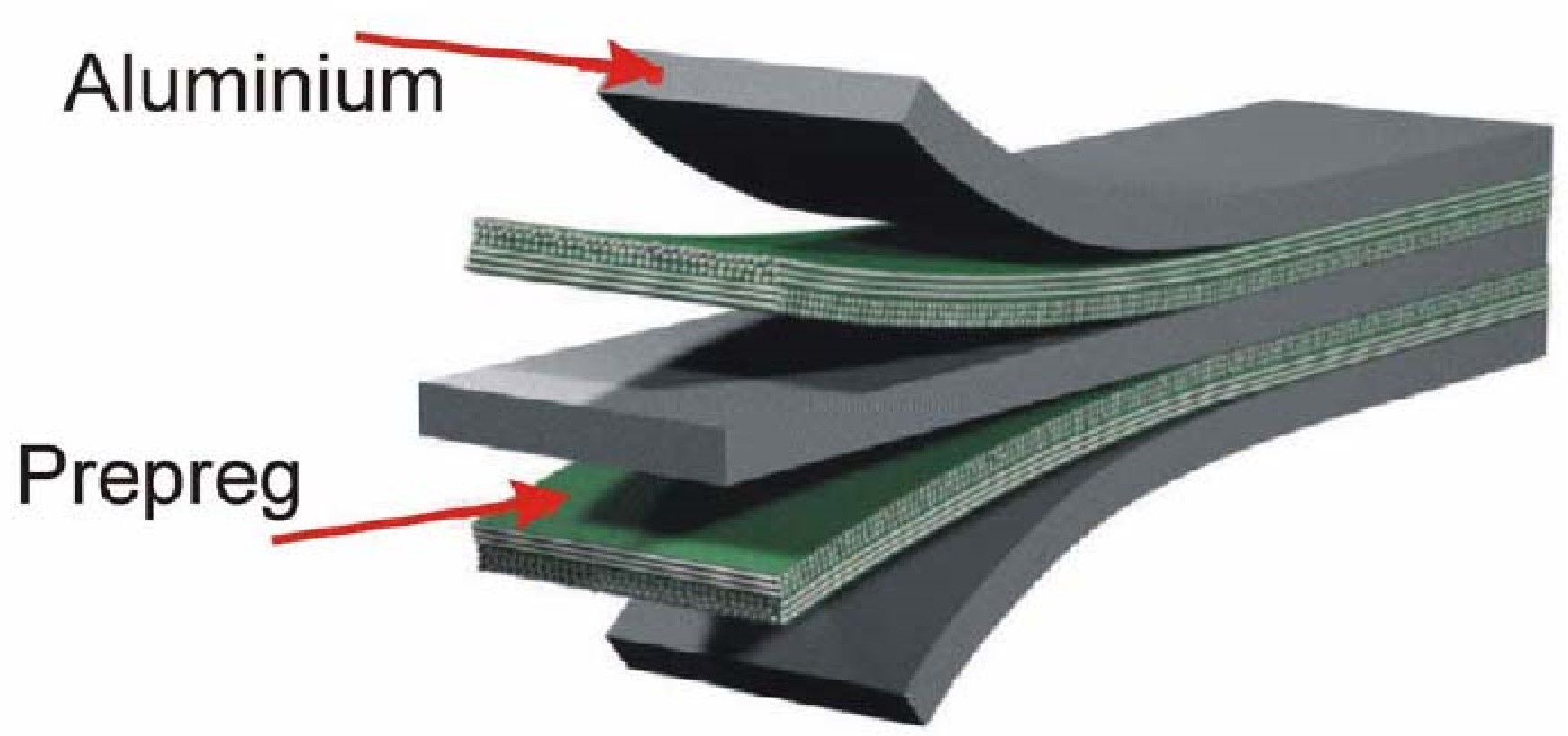
Objectifs :
L’apprenant sera capable :
- d’expliquer la constitution du GLARE,
- de citer les principaux avantages et inconvénients de ce matériau,
- de décrire les principales contraintes en production.
L’association aluminium et composite permet d’utiliser un matériau associant une bonne tenue aux chocs (grâce à l’aluminium), une grande résistance à la charge, une bonne tenue à la fatigue et donc une grande résistance à la propagation de fissures (grâce au composite).
Ce nouveau matériau (le GLARE : GLass Aluminium REinforced) nécessite un bon collage entre les plis composites et les tôles métalliques.
En faisant varier l’orientation des fibres des couches composites et les épaisseurs des deux matériaux, il est possible d’élaborer des matériaux adaptables aux propriétés souhaitées. Néanmoins il n’est pas avantageux partout car il présente des caractéristiques de rigidité inférieure de 15% à celles de la tôle d’aluminium seule.
Comme le composite, le GLARE n’est pas transformable après polymérisation et l’aspect stratifié le rend sensible aux délaminages lors de chocs sur la tranche.
A l’usinage il présente également quelques inconvénients très connus chez les composites : usure des outils et dégagement de fibrilles de verre.